Master Alloys
Improve Recovery and Production Using Shapiro Master Alloys
Master Alloys
September 14, 2021
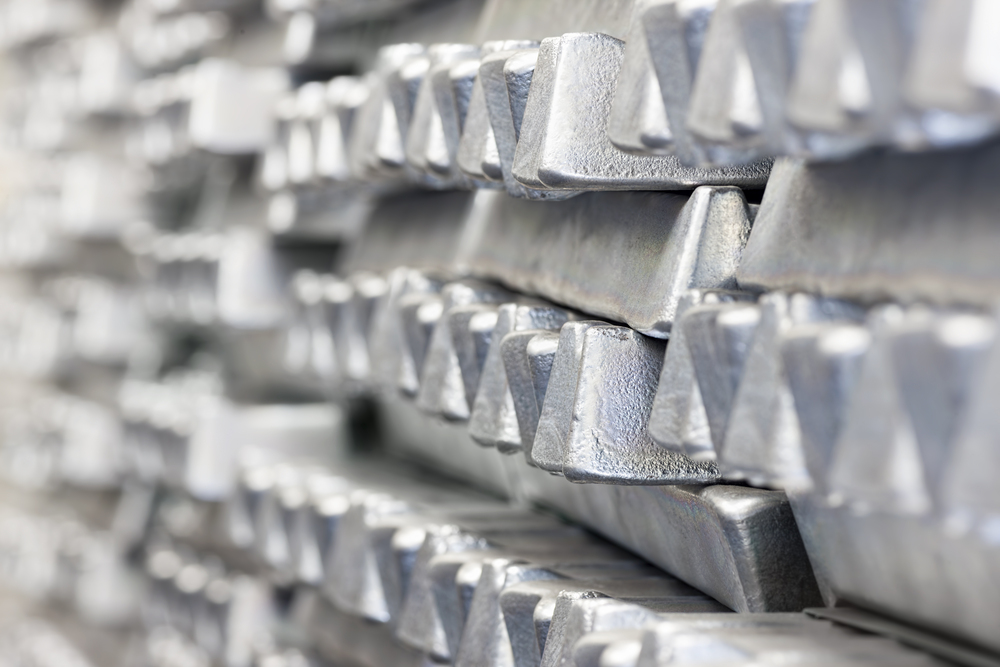
Improve Recovery and Production Using Shapiro Master Alloys
Across all kinds of industries, people value purity. Pure products are consistent and predictable, reducing guesswork about what they contain or how they’ve been modified. There are many benefits to using master alloys for manufacturing, though, even compared to pure metals.
Unfortunately, not all alloys offer the right composition to maximize quality, so it’s important to identify options that offer dependable recovery rates and keep the operation running smoothly. Choosing aluminum master alloys with the right size and composition for your process will yield high recovery rates, keep furnace down-time to a minimum, and maximize productivity by increasing throughput.
What Is Recovery Rate in Manufacturing?
Recovery rate is one of the most important indexes of aluminum master alloys. It is a function that measures the weight and size of the melt at various times throughout the process to determine how much of the additive (such as silicon or magnesium) and the primary metal is lost. A high recovery rate indicates that less of the raw material is being lost throughout the melting, molding, and manufacturing process.
Why Is Recovery Rate Important?
Improved metal recovery increases the throughput of the production cycle. High recovery rates are indicative of cost-effective processes and efficient performance, as the same amount of raw source material stretches further. Consistent recovery rates also empower greater control of the ultimate quality and chemical composition of the finished product, because there is reduced need to make adjustments on the fly. The melt rate and metal recovery rate help separate next-generation master alloys from traditional master alloys.
How Master Alloys Improve Recovery Rates
A master alloy is a base metal that’s been combined with one or two other elements. Aluminum master alloys, for example, might include another element, like silicon or magnesium, that changes the properties of the raw material.
There are many benefits of metal alloys for manufacturing, but potential issues with consistency often lead to tempermental melting, low recovery rates, and wasteful loss of raw materials if low-quality alloys are selected.
Next-generation master alloys solve those types of problems by offering predictable melting that maximizes recovery rates. When material loss decreases, throughput rises and an operation spends the same amount to produce much more. Recovery rate helps measure the efficiency of the process.
Master alloys for manufacturing offer multiple technical and economical advantages, including:
- Lower error rates and increased accuracy (due to the decreased reliance on the furnace operator)
- Reduced environmental footprint (less water usage, mining waste, and energy consumption)
- Decreased energy consumption due to lower melting rates
- Increased yields over pure metals
When combined with the high recovery rates of master alloys, these benefits allow manufacturers to produce quality products at a fraction of the cost.
Aluminum Master Alloys and Recovery Rate
Master alloys for manufacturing offer financial and technical benefits over pure metals, including serious cost savings and better efficiency. Pure metals often show poor yield and high losses, especially when the correct melting point is not achieved.
Adding additional elements like magnesium or silicon to make an aluminum master alloy allows the raw material to dissolve more quickly at lower temperatures. This saves energy, eliminates waste, and accelerates production, but the mix must be consistent to ensure predictable results.
Uniform materials dramatically reduce the burden on furnace operators, who would otherwise be tasked with adding additional blocks or materials to make up for lost material. These operators no longer need to babysit the melt when using aluminum master alloys with proper ratios. Instead of working to mix and blend materials on the fly, the staff is freed up to dedicate time to other tasks. The workload is further reduced by aluminum-rich sows in large sizes.
How to Choose the Right Aluminum Master Alloys
Traditional master alloys might be small, 30-pound ingots of a 90% silicon, 10% aluminum blend. Shapiro Master Alloys does something different, offering massive sows of alloy that is 93%-97% aluminum. Using such a significant amount of aluminum allows our partners to meet their recycled content goals without relying on metals that fall short of their specifications for quality and consistency.
Shapiro maximizes the benefit by delivering our master alloys in 1,000- or 2,000-pound sows, a feature distinct in our industry. This sizing and composition of our master alloys further helps your production run more efficiently and maximize your recovery rates. When it comes to choosing the raw materials for your manufacturing operations, next-generation master alloys offer you the best of both worlds.
Aluminum Master Alloys for Manufacturing
Metallurgical experts from Shapiro Master Alloys have specific expertise in the blending and creation of master alloys. We leverage that experience to produce larger sows of alloys that have been blended to help our partners reduce or eliminate their dependence on pure aluminum. Get in touch with one of our experts to learn more about how our aluminum master alloys can improve recovery rates, reduce furnace down-time, and let you pour more metal.