News
Aluminum-Silicon Alloy Production FAQ
News
November 1, 2024
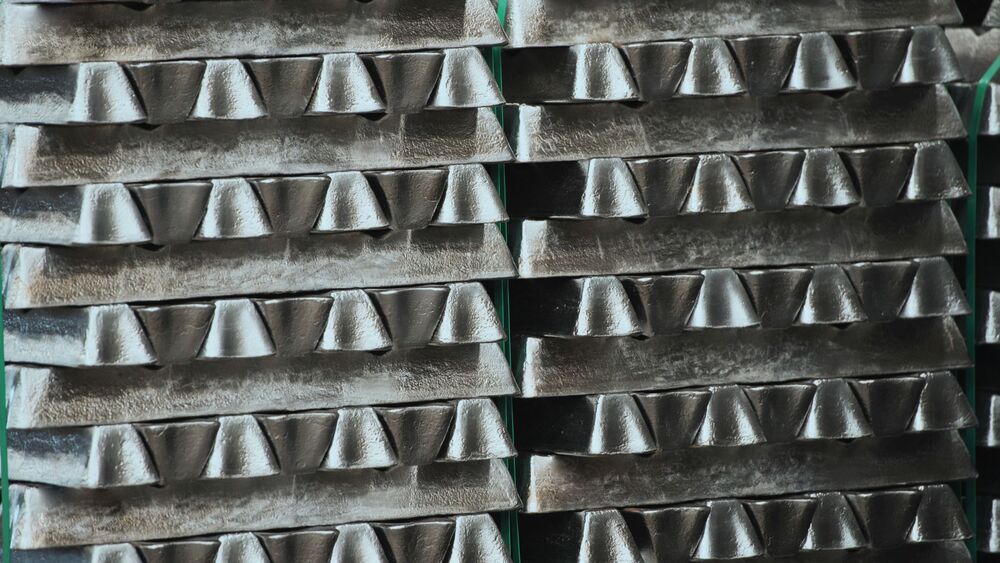
1. What are the environmental benefits of using recycled aluminum (secondary aluminum) compared to producing primary aluminum?
Producing primary aluminum through the Hall–Héroult process requires significant energy and generates substantial CO2 emissions (12–16.5 tCO2eq/t Al produced). In contrast, recycling aluminum consumes only about 5% of the energy needed for primary production and results in considerably lower emissions (0.6 tCO2eq/t Al). Additionally, secondary aluminum production avoids the generation of substantial solid-liquid waste, such as bauxite residue, associated with primary production.
2. How does the carbon footprint of producing primary silicon compare to using recycled aluminum-silicon alloys?
Similar to aluminum, primary silicon production, primarily through the carbothermic reduction of quartz, carries a hefty carbon footprint of ~11.3 t CO2e/t Si. Utilizing recycled aluminum-silicon alloys significantly reduces this footprint, contributing to a more sustainable circular economy
3. What are the economic and environmental advantages of manufacturing aluminum-silicon alloys from scrap?
Producing aluminum-silicon alloys from scrap offers several advantages:
- Cost-effectiveness: Scrap aluminum is generally cheaper than primary aluminum and silicon.
- Energy savings: Melting scrap requires less energy than producing primary metals.
- Reduced environmental impact: Lower energy consumption and reliance on recycled materials translate to reduced greenhouse gas emissions and waste generation.
4. What are the two main furnace technologies used for melting aluminum scrap, and how do they differ in terms of scrap quality?
The two primary furnace technologies used for melting aluminum scrap are:
- Rotary furnaces: These furnaces are well-suited for handling lower-quality scrap, due to their robust design and melting capabilities.
- Reverberatory furnaces: These furnaces are more appropriate for melting cleaner scrap, as their design prioritizes efficient heat transfer and minimal contamination.
5. How does the energy efficiency of rotary and reverberatory furnaces impact CO2 emissions?
Rotary furnaces typically have a higher energy efficiency (around 95%) than reverberatory furnaces (around 40%). This difference in efficiency translates to different CO2 emissions per ton of metal melted. For instance, in the provided data, melting aluminum scrap in a rotary furnace results in 0.39 tons of CO2 emissions per ton of metal, while melting in a reverberatory furnace generates 0.92 tons of CO2 emissions per ton of metal.
6. What is the overall CO2 footprint of producing aluminum-7% silicon alloy using primary vs. secondary materials in rotary furnaces?
Using primary aluminum and silicon in a rotary furnace to produce aluminum-7% silicon alloy results in a CO2 footprint of 14.48 tons per ton of metal. Conversely, using scrap aluminum and silicon reduces this footprint to 0.6 tons per ton of metal. This significant difference highlights the environmental benefits of utilizing secondary materials.
7. How does the choice of furnace technology affect the overall CO2 emissions when producing Al-7Si alloy from both primary and secondary sources?
The choice of furnace technology can influence the overall CO2 emissions. While both rotary and reverberatory furnaces result in considerably lower emissions when using secondary materials, the higher energy efficiency of rotary furnaces generally leads to lower emissions overall, regardless of the material source.
8. What other environmental factors, besides CO2 emissions, are relevant when comparing primary and secondary aluminum production?
Beyond CO2 emissions, other environmental factors to consider include:
- Solid waste generation: Primary aluminum production generates significant amounts of spent pot lining and bauxite residue, while secondary production primarily generates aluminum dross, which can be further processed and recycled.
- Water usage: Primary aluminum production involves substantial water consumption during the alumina extraction process, while secondary production requires minimal water.
- Fluorocarbon emissions: Primary aluminum production releases perfluorocarbons (PFCs), potent greenhouse gases, while secondary production generally avoids these emissions.